Taps and clangs of hammers hitting metal. The warm, orange glow of coals and iron. Fine black dust in the air and on gloved hands.
In 2025 at Cannonsburgh Village, blacksmithing is anything but obsolete.
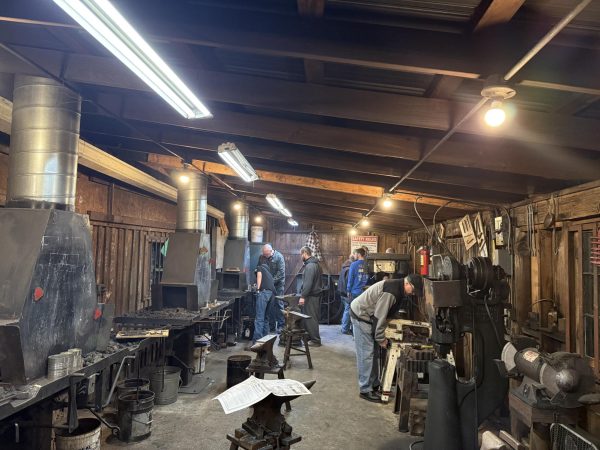
The village was assembled in 1976 for Murfreesboro, Tennessee’s U.S. bicentennial celebration. A popular field trip destination for local elementary students and the home of the World’s Largest Cedar bucket, the quaint village’s historic buildings include a one-room schoolhouse, a general store and a doctor’s office. Not all the buildings are relics. Brides still walk down the aisle of the tiny chapel. And then there’s the blacksmith shop, very much open for business.
The Rutherford County Blacksmiths Association – a rotating assembly of novices and old hands – keeps the shop busy. With “Green Coal” classes for beginners every Tuesday and Thursday night, plus open forge sessions on Wednesdays for more experienced smiths, the coals smolder throughout the week. At monthly business meetings, the agenda always includes time for showing off new creations.
The shop is more than a building — it’s a brotherhood.
Inside, fluorescent lights hang above, illuminating the forges. The dark wood and dark iron add to the 19th century aesthetic.The heat brings on sweat, even in winter.
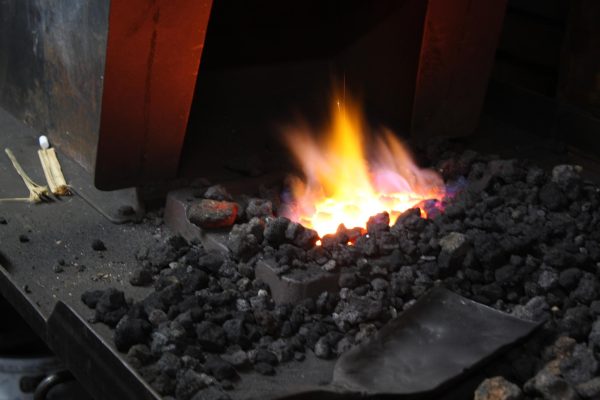
“In the summertime, we die,” James Jones said. “It’s really bad. Of course, we got big fans, and we keep those windows open to draw air. But, yeah, it’s crazy hot in here in summer.”
Jones, the vice president of the association, has a bushy beard and a warm laugh. He started his blacksmithing journey about three years ago when his wife signed him up as a Father’s Day gift. Even before he entered the forge, he was a craftsman.
“I’ve always been a maker,” Jones said. “My wife and I, before our little girl, we were big into cosplay and we made all of our own costumes.”
Like other RCBA students, Jones started in the Green Coal program — a series of 13 projects that teaches skills to use on every future piece. Students apply heat and force to draw out, taper, and shape steel.
“It’s really neat to watch the new students come to that realization once they graduate Green Coal, and they see a seasoned blacksmith teaching a complicated project, and they see the pieces or the elements, and they go, ‘I know how to do all of that,’” Jones said.
On a November night at the forge, seasoned craftsmen assisted newer members, including three first-timers.
“This is a brand new student,” said Matt Clarady, RCBA president, nodding toward a recent recruit. The student leaned toward a volunteer teacher to better hear his instructions over the din. “He had a safety talk tonight, paid his fees, and he’s gonna learn how to build a fire. That’s his first project.”
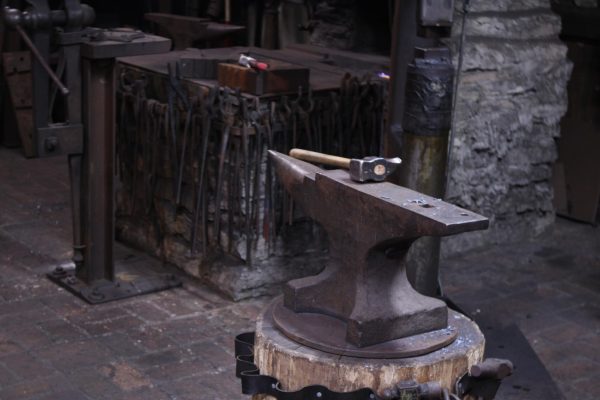
The new student will spend the next few months, as much time as he needs, forging various hooks and tongs, a ladle, and the final Green Coal project, a fire poker.
Each station in the shop contains a two-sided forge — a hearth for burning heat-producing fuel. The RCBA uses coke, a refined coal product with a higher carbon level.
“A lot of people use coal,” Clarady said. “Coke is refined and smokes less, which our neighbors appreciate. And so does the fire department, because it doesn’t look like something’s on fire.”
The stations are also equipped with anvils perched on stumps, vises and other tools smiths have used for centuries.
In recent years, membership increased due to the popularity of “Forged in Fire,” a History Channel reality competition show where bladesmiths compete in prescribed challenges creating weapons. This forge’s focus isn’t on weaponry. While some bladesmithing takes place, (a recent knife workshop was popular with more advanced smiths,) members are making kitchen knives, not weapons. They’re also forging garden tools and sconces for the dining room wall. They want to make gifts and things that will last.
“I love making things and giving them away,” Clint “Buzz” Busbee said. “I like making Christmas things for people … I think it means much more to somebody than just going and buying something, right?”
Busbee scrolled through photos on his phone, beaming over past projects like he was showing off grandchildren. Much of his work is decorative — like a bird bath, a table and a treasure chest. Organic motifs of flowers and leaves appear in his creations.
“I like vines, and I like a lot of nature and stuff,” Busbee said. “Because, first of all, I’m terrible at measuring, and so it just comes more natural for me. I can make these other things, but I don’t get as much enjoyment as I do with the nature stuff.”
Busbee traveled around the forge, checking in with students and instructors, filling the air with laughter and chatter between clangs.
“I enjoy the camaraderie and the hands-on work,” he said. “When you do this, you’re one of us.”
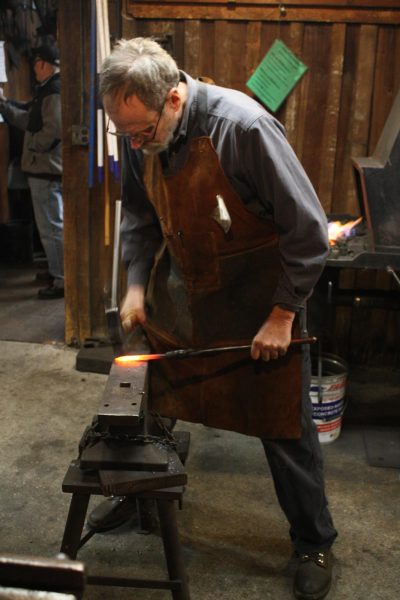
Busbee isn’t the only strong presence: Ron Nichols may be quiet, but his influence reverberates through the shop.
Nichols started working with metal as a teenager in the 1960s, when he sold his cows to buy a welder. He joined the group in 1990. He has been certified as a level three instructor — the highest certification issued by the Artist-Blacksmith’s Association of North America. It’s an impressive honor, but Nichols preferred talking about a recent creative project. He found unlikely inspiration in a hand-stitched quilt.
“I forged the alphabet,” Nichols said. “I had never seen an alphabet forged before. It was very rewarding.”
Nichols can shape almost anything from iron, but in his role as volunteer instructor, he helps beginners discover life-shaping confidence with every swing of the hammer.
“I’ve built a lot of stuff in my life,” Nichols said. “But it’s so rewarding so often, to get a young lad to come through here, and they just never hit a home run in their life. They just never got an A-plus on their grades, and they click. Seeing that success come around and mature through that young person is probably the most rewarding thing I’ve ever had happen.”
To contact the editor, email [email protected].
Follow Sidelines on Facebook at Facebook.com/MTSUSidelines, on X @mtsusidelines and Instagram @mtsusidelines. Sign up for our weekly newsletter here.